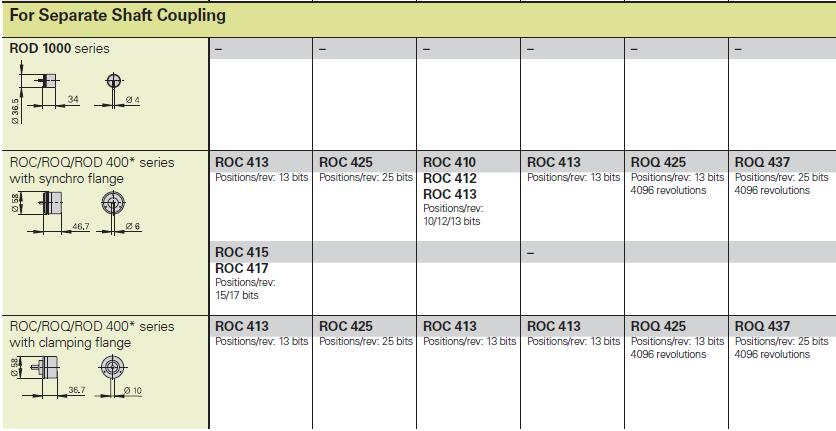
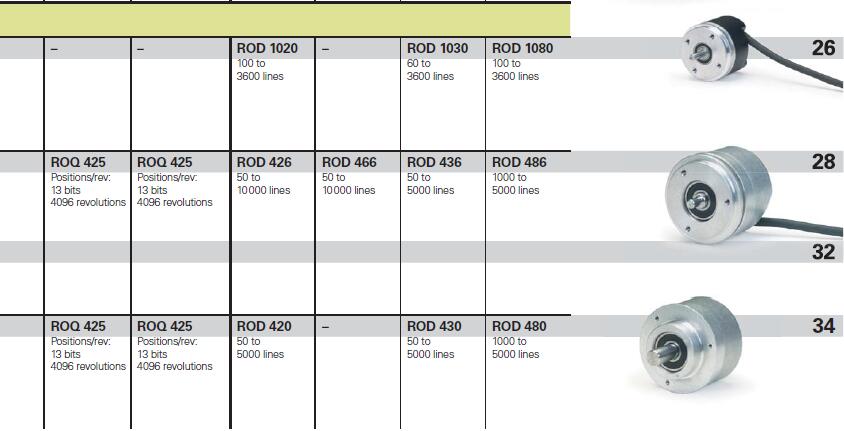
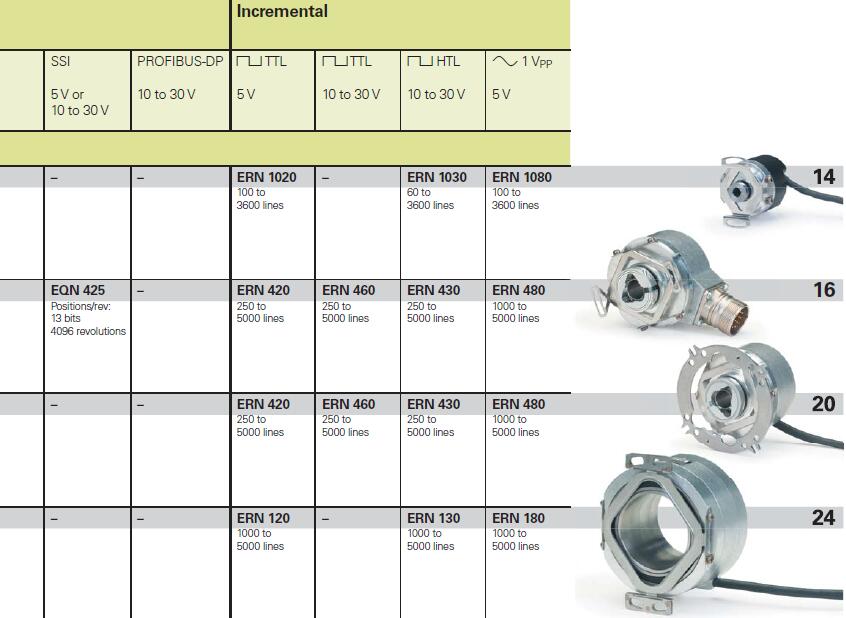
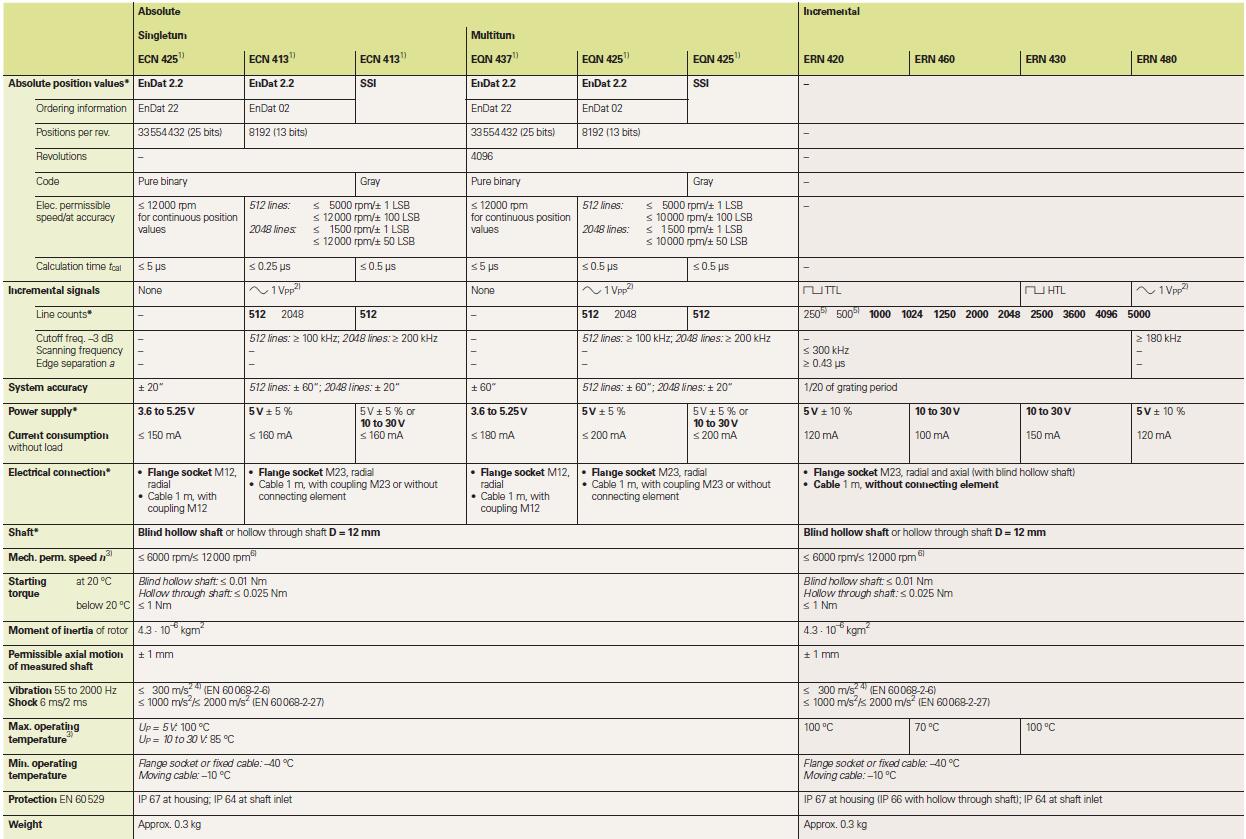
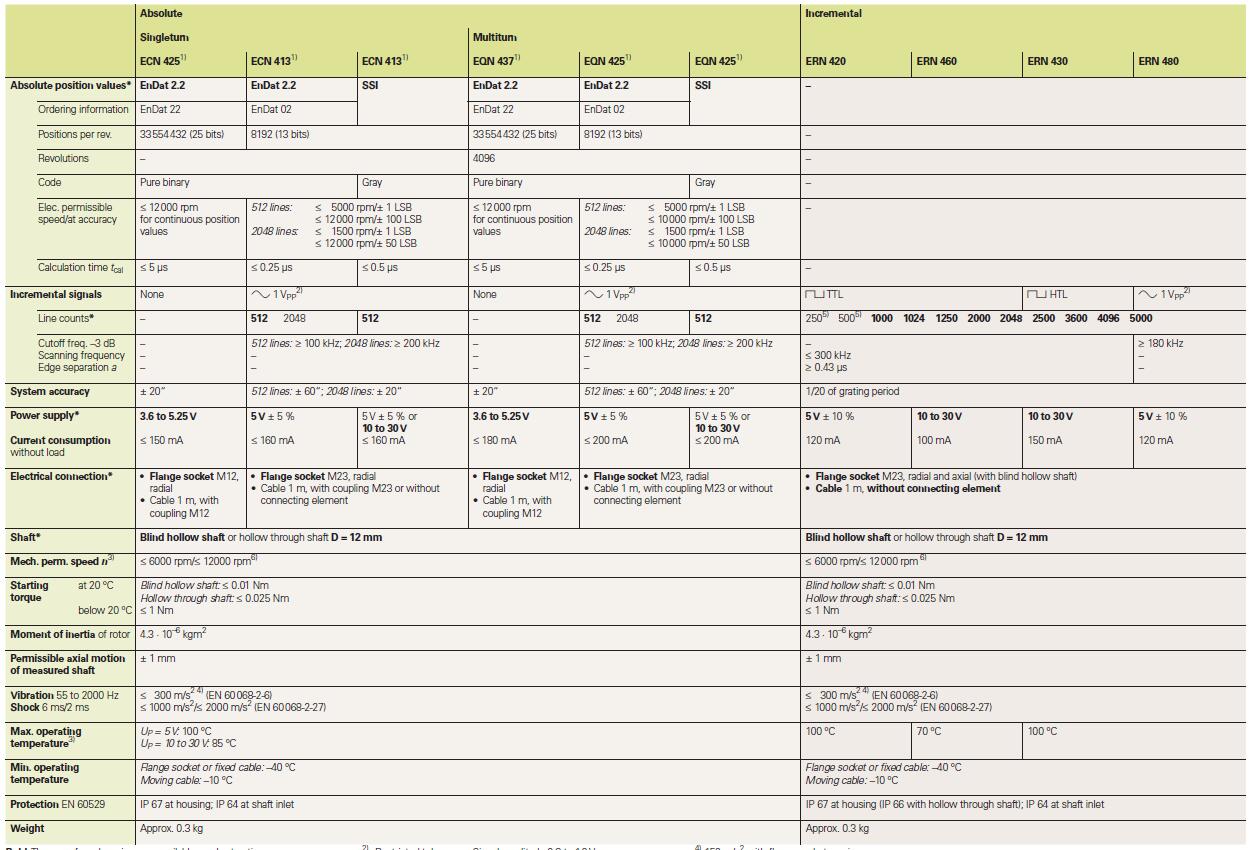
Measuring Principles
Measuring Standard Measuring Methods
HEIDENHAIN encoders with optical
scanning incorporate measuring standards
of periodic structures known as graduations.
These graduations are applied to a carrier
substrate of glass or steel.
These precision graduations are
manufactured in various photolithographic
processes. Graduations are fabricated
from:
extremely hard chromium lines on glass,
matte-etched lines on gold-plated steel
tape, or
three-dimensional structures on glass or
steel substrates.
The photolithographic manufacturing
processes developed by HEIDENHAIN
produce grating periods of typically 50 μm
to 4 μm.
These processes permit very fi ne grating
periods and are characterized by a high
defi nition and homogeneity of the line
edges. Together with the photoelectric
scanning method, this high edge defi nition
is a precondition for the high quality of the
output signals.
The master graduations are manufactured
by HEIDENHAIN on custom-built highprecision
ruling machines.
••
•
With absolute measuring methods, the
position value is available from the encoder
immediately upon switch-on and can be
called at any time by the subsequent
electronics. There is no need to move the
axes to fi nd the reference position. The
absolute position information is read from
the disk graduation, which consists of
several parallel graduation tracks.
The track with the fi nest grating period is
interpolated for the position value and at
the same time is used to generate an
optional incremental signal.
In singleturn encoders the absolute
position information repeats itself with
every revolution. Multiturn encoders can
also distinguish between revolutions.
With incremental measuring methods,
the graduation consists of a periodic
grating structure. The position information
is obtained by counting the individual
increments (measuring steps) from some
point of origin. Since an absolute reference
is required to ascertain positions, the
graduated disks are provided with an
additional track that bears a reference
mark.
The absolute position established by the
reference mark is gated with exactly one
measuring step.
The reference mark must therefore be
scanned to establish an absolute reference
or to fi nd the last selected datum.
Scanning Methods
Photoelectric Scanning
Most HEIDENHAIN encoders operate
using the principle of photoelectric
scanning. The photoelectric scanning of a
measuring standard is contact-free, and
therefore without wear. This method
detects even very fi ne lines, no more than
a few microns wide, and generates output
signals with very small signal periods.
The ECN, EQN, ERN and ROC, ROQ, ROD
rotary encoders use the imaging scanning
principle.
Put simply, the imaging scanning principle
functions by means of projected-light
signal generation: two graduations with
equal grating periods are moved relative to
each other—the scale and the scanning
reticle. The carrier material of the scanning
reticle is transparent, whereas the
graduation on the measuring standard may
be applied to a transparent or refl ective
surface.
When parallel light passes through a
grating, light and dark surfaces are
projected at a certain distance. An index
grating with the same grating period is
located here. When the two gratings move
relative to each other, the incident light is
modulated. If the gaps in the gratings are
aligned, light passes through. If the lines of
one grating coincide with the gaps of the
other, no light passes through. Photovoltaic
cells convert these variations in light
intensity into nearly sinusoidal electrical
signals. Practical mounting tolerances for
encoders with the imaging scanning
principle are achieved with grating periods
of 10 μm and larger.
Photoelectric scanning according to the imaging scanning principle
LED light source
Condenser lens
Scanning reticle
Measuring standard
Photocells
I90° and I270°
photocells are
not shown
Accuracy
The accuracy of position measurement
with rotary encoders is mainly determined
by:
the directional deviation of the radial
grating,
the eccentricity of the graduated disk to
the bearing,
the radial deviation of the bearing,
the error resulting from the connection
with a shaft coupling (on rotary encoders
with stator coupling this error lies within
the system accuracy),
the interpolation error during signal
processing in the integrated or external
interpolation and digitizing electronics.
For incremental rotary encoders with line
counts up to 5000:
The maximum directional deviation at
20 °C ambient temperature and slow
speed (scanning frequency between
1 kHz and 2 kHz) lies within
± 18° mech. · 3600 [angular seconds]
which equals
± 1 grating period.
ROD rotary encoders with 6000 to 10000
signal periods per revolution have a system
accuracy of ±12 angular seconds.